Introduction
Design of Capacitor Charging Power Supplies: In order to power laser flashlamps, pulse forming networks, and other energy storage capacitor applications, the capacitor is charged up in voltage, then regulated. This creates an unusual and different situation from conventional fixed load. Consider the case where the capacitor is fully discharged. When the power supply is turned on, then virtually no power can be delivered because the initial voltage across the capacitor is zero or very low. The output current is limited by the rating of the output components, so the delivered power is low. As the capacitor charges, linearly if the output current is constant, then more power may be delivered. Just before the end of the charging cycle, maximum power is delivered and this power is twice the average power. For example, if the charger is rated at 1,000 joules per second, the initial power is zero watts, and the final power is 2,000 watts, to give an average power of 1,000 watts over a complete charging cycle. The power wave shape is a sawtooth ramp and its rms value is 15.5% more than the average current, but more importantly, if the capacitor energy is large, the input power draw may double causing blown fuses or power limitations. Another consequence of this ramp is a reduced power capability as the output voltage is reduced. In many cases a power factor corrector is added and to keep a fairly constant sinusoidal input current, the energy stored in the reservoir boosted voltage capacitor must be several times that of the energy storage capacitor. This means a large value and size of reservoir must be used. AMI has come up with some innovative solutions to solve these issues and improve efficiency, reduce size, and improve the power quality.
The “Gearshifter”
Just as your automobile starts off in a low gear to get going more quickly, the output current is doubled at voltages under 50% of full charge voltage by paralleling two output windings and rectifiers. This allows full power to be delivered at 50% of the output voltage. The figures show the advantage in charge time and power draw. Above 50% of full charge voltage, the windings are automatically configured in series to create the optimum transformer ratio. AMI power supplies with this feature can therefore work efficiently over a large dynamic range of capacitor voltage. This is a unique patented (Patent 5,461,297) feature of AM’s design of capacitor charging power supplies.

Figure 1
Power Factor Corrector
UL and IEC specify harmonic current limits and generally this requires a power factor corrector to ensure that the input current flow matches the input voltage cycles. Standard correctors are designed expecting a consistent load current, so a slow loop of bandwidth typically 8 Hz is used to set the power draw. This loop can get confused with the pulsed load and results in distortion as shown.
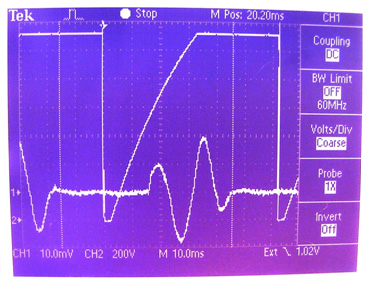
Figure 2
The damped oscillation shows the slow loop trying to cope with the varying demand during the charge cycle.
AMI has a technique of adjusting the power rate of charge so that full charge is reached just before the firing of the laser. (Patent 6,087,811). This reduces the current draw and smooths it out over the cycle. The storage capacitor is made of sufficient size so that the slow loop can cope. The reduced currents and smooth sinusoidal draw is shown below.
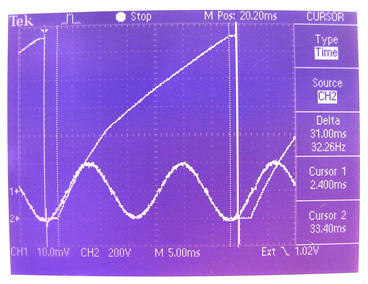
Figure 3
A bonus to this design of capacitor charging power supplies is a 5 to 10% efficiency improvement due to the lower currents (i squared R losses). In the ramp shape, the increased first gear slope can be clearly seen on the ramp, and full charge (flat potion) occurs just before discharge.
EMC
AMI power supplies incorporate input and output filters to minimize EMI. The input filter incorporates a coupled choke to provide high common made rejection, line-to-line capacitors and values of line-to-ground capacitors as high as possible, yet meeting the leakage current requirements. A custom full-wave bridge topology is used to minimize ripple, and split bobbin transformers are used to minimize primary to secondary capacitance with excellent isolation. The high voltage output has high frequency decoupling capacitors with both a balum and a series choke arranged so that a resonant circuit cannot be formed with varying customer load impedances. A high frequency chassis shield decoupling capacitor is normally fitted to return any capacitively induced noise to the local ground. The efficient pin power transistor heat sinks are isolated in the center of the unit and air cooled so that noise is not coupled into chassis. Care is taken not to couple the fast moving waveforms into the chassis through mounting capacitance.
The Gearshifter and rate control measures described above minimize flicker. By maintaining a smooth flow of power throughout the charging cycle until the time of discharge, the input voltage fluctuations causing flicker are low For example in the input current waveform of Figure 3, there is no visible current change and therefore little flicker.
© Analog Modules Inc. This post may be reproduced in its entirety without editing.